2020年11月27日,清华大学机械工程系助理教授赵沧作为独立第一作者和共同通讯作者在Science(《科学》)上以“Critical instability at moving keyhole tip generates porosity in laser melting”(激光加热中匙孔根部的临界失稳产生气泡缺陷)为题发表了关于金属激光3D打印的最新成果。该项研究起于宏观工艺,立于微观细节。宏观层面上,在激光功率-扫描速率空间中,匙孔气泡缺陷区域的边界清晰而平滑,且受金属粉末加入的影响甚微。在微观层面上,这些气泡缺陷的形成与匙孔根部的临界失稳有关;后者可以在熔池中释放出声波(冲击波),进而驱动气泡快速远离匙孔、并被凝固前端捕捉。
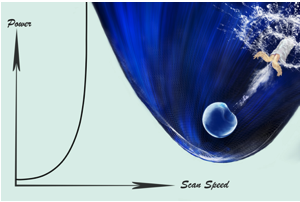
图1. 关于匙孔气泡区边界和气泡缺陷起源的艺术插图。左侧,在激光功率-扫描速率空间中,匙孔气泡区边界清晰而平滑。右侧,在该边界附近,匙孔根部的临界失稳释放出声波(冲击波),进而驱动气泡快速远离匙孔。当气泡被凝固前端捕捉,便成了缺陷。(插图设计者:清华大学冯叶;版权所有者:清华大学赵沧)
研究背景
激光粉末床熔融成形是金属3D打印中广泛使用的一门技术。在一个典型的成形过程中,基于一个离散化的三维数字模型,高功率激光快速扫过一层金属粉末颗粒(厚度为几十到一百微米),有选择性地将粉末颗粒熔化和融合。因此,该技术在复杂几何结构零部件的直接制造方面具有无与伦比的优势。但是,气泡总是如影如随,损害零部件的抗腐蚀、抗疲劳性能,因此,往往在尖端应用领域(如航空发动机涡轮叶片)成为阿喀琉斯之踵。一般认为,在激光粉末床熔融成形中,激光加热处于传导模式,而匙孔的广泛存在性直到2019年初才被揭示(Science, 2019, 363(6429): 849-852)。这意味着,匙孔作为气泡缺陷的一种可能来源,不可被忽视。
问题的提出
在激光粉末床熔融成形中,“激光功率-扫描速率”工艺图谱将产品质量(如相对密度)与工艺参数(亦包括扫描间距)直接联系起来,便于3D打印机的用户查询和参考。然而,在该图谱中,几个关键部分仍然缺失,以至于无法准确确定打印工艺的优化窗口。其中一个就是匙孔气泡缺陷区域的边界。该边界将划分出稳定熔化区和匙孔气泡区,而全致密成形仅存在于前者。所以,问题一:匙孔气泡区的边界是否可以被清晰定义并且具有重复性?进一步,在激光粉末床熔融成形中,一般认为,粉末颗粒的存在会产生更大的匙孔涨落和更多的气泡。但是,该认识一直停留在定性的描述上,粉末颗粒的作用缺乏定量化的评价和分析。这是第二个问题,关注点集中在粉末颗粒对于匙孔气泡区边界的影响。第三个问题是关于匙孔气泡缺陷的起源。目前的知识边界:匙孔气泡的产生与匙孔的孔壁失稳有关;匙孔的根部在多种力(比如马兰戈尼对流、反冲压力等)的综合作用下被掐掉,如果被凝固前端钉扎,便成了一种微观缺陷。该理解相对宽泛而缺乏细节,有必要深究,特别关注匙孔气泡区边界附近气泡的形成和最初的运动。
匙孔气泡缺陷区域的边界
在“激光功率-扫描速率”工艺图谱中,匙孔气泡缺陷区域的边界呈现出出乎意料的清晰和平滑。粉末颗粒的加入,将匙孔气泡区略微扩大了些。远离该区域的边界,比如在恒定的激光功率下降低扫描速率,可辨识的气泡的最大尺寸趋于变大。随着激光功率的减小,匙孔气泡区的边界对扫描速率愈发敏感(特别是当存在粉末颗粒时),且渐进于一个功率阈值
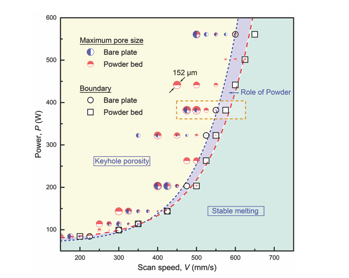
图2. 激光熔融成形中的匙孔气泡缺陷区域的边界。浅黄色区域为匙孔气泡缺陷区,浅绿色区域为稳定熔化区,浅紫色区域呈现了金属粉末的作用。加入金属粉末增加了匙孔的不稳定性,因此拓宽了匙孔气泡缺陷区。(经许可转载自C Zhao et al., SCIENCE, Nov 27 2020)
金属粉末颗粒的作用
在匙孔气泡缺陷区域边界的低端(低激光功率-扫描速率),匙孔深度的相对涨落随着激光功率和扫描速率的减小急剧增加。在存在粉末颗粒的情况下,该现象特别显著,相对涨落甚至超过1。这意味着,激光钻孔有时候可以远超平均值,而在匙孔的底部残留下气泡。换个角度,粉末颗粒(亦包括溅射颗粒)可能间或进入到激光束线中,以至于匙孔接受到的激光能量发生突变,引起局域温度和反冲压力的瞬时下降,最终造成匙孔深度的涨落。有意思的是,在整个匙孔气泡区的边界上,无论粉末颗粒存在与否,匙孔深度与前壁倾斜角的正切值呈现出一致的线性关系;其斜率被定义为匙孔气泡常数,显著大于之前定义的激光束斑有效尺寸(Science, 2019, 363(6429): 849-852)。
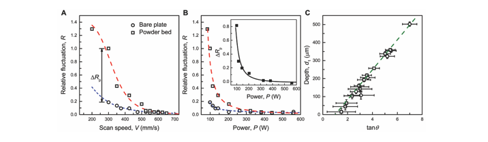
图3. 激光熔融成形中粉末颗粒的作用。在匙孔气泡区边界低激光功率-扫描速率的一端,金属颗粒的加入显著增加匙孔深度的相对涨落。在整个边界上,无论颗粒存在与否,匙孔深度与前壁倾斜角的正切值呈现出一致的线性关系。(经许可转载自C Zhao et al., SCIENCE, Nov 27 2020)
匙孔气泡缺陷的起源
在匙孔气泡缺陷区域的边界附近,气泡往往小而圆。它们的形成及最初的运动与匙孔根部的临界失稳有关。匙孔前后壁的碰撞产生气泡和微流喷射。微流喷射随后促进气泡的坍塌、分裂和反弹。在这个过程中,气泡悬浮于熔池中,几乎静止。随着气泡的坍塌和反弹,匙孔的根部,特别是靠近气泡的一侧,几乎同步变形,呈现出针状。之后,该针状根部发生爆炸式的膨胀,同时在下面的熔池中释放出声波(冲击波),进而驱动气泡快速远离匙孔。当气泡被凝固前端捕捉,便成了缺陷。此外,在匙孔气泡区边界的低端共存着第二种机理。匙孔剧烈涨落(特别是回缩,在粉末颗粒存在的情况下尤甚),为气泡创造出足够的时间以等待凝固前端的捕捉。在等待的过程中,气泡可能被局域的熔体流动产生的拖拽力加速并远离匙孔。
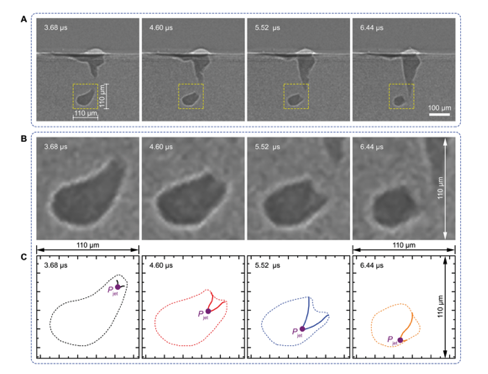
图4. 匙孔气泡与微流喷射。匙孔前后壁的碰撞产生气泡和微流喷射。微流喷射随后促进气泡形貌的演化。在这个过程中,气泡悬浮于熔池中,几乎静止。(经许可转载自C Zhao et al., SCIENCE, Nov 27 2020)
工作意义
该研究工作为未来无气泡全致密金属激光3D打印提供了理论支撑和技术支持。宏观上,优化了打印的工艺窗口。微观上,发现了一种新的匙孔气泡缺陷起源机理。
论文贡献
论文独立第一作者为清华大学机械工程系和先进成形制造教育部重点实验室的赵沧。论文共同通讯作者为清华大学的赵沧、卡内基梅隆大学的Anthony Rollett和弗吉尼亚大学的Tao Sun。论文合作者还包括阿贡国家实验室和犹他大学的研究人员。该项工作得到了清华大学长聘教授都东团队的支持和清华大学人才引进经费的资助。
赵沧,清华大学助理教授、博士生导师,机械工程系都东教授团队成员。主要研究方向为金属增材制造关键机理的探索。完成了美国先进光子源金属增材制造同步辐射在线监测平台的设计和研制,并深入研究了匙孔演化、液滴飞溅、匙孔气泡等基础问题。严格定义了激光加热的三种模式,指出了增材制造中匙孔的广泛存在性;发现了一种新的快速飞溅机理;确立了匙孔气泡缺陷区域的边界,发现了一种新的气泡缺陷起源机理。代表性论文包括《科学》(Science,两篇)、《物理评论X》(Physical Review X)等。曾获得中国科学院院长优秀奖、美国阿贡国家实验室博士后杰出贡献奖等。
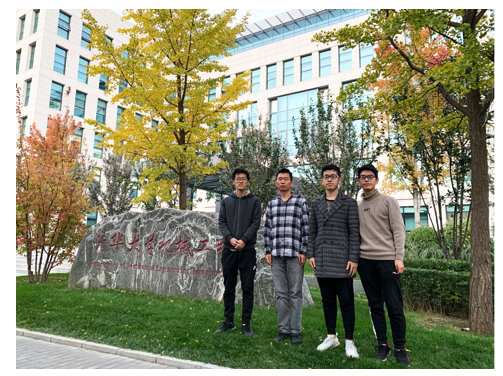
图5. 机械系助理教授赵沧(左二)和课题组的学生们
论文链接:
https://science.sciencemag.org/cgi/doi/10.1126/science.abd1587
See: Cang Zhao 1*, Niranjan D. Parab 2, Xuxiao Li 3, Kamel Fezzaa 2, Wenda Tan 3, Anthony D. Rollett 4*, Tao Sun 5*, "Critical instability at moving keyhole tip generates porosity in laser melting", SCIENCE, Nov 27 2020 (DOI: 10.1126/science. abd1587)
Author affiliations: 1 Tsinghua University, 2 Argonne National Laboratory, 3 University of Utah, 4 Carnegie Mellon University, 5 University of Virginia
Correspondence: cangzhao@tsinghua.edu.cn, rollett@andrew.cmu.edu, ts7qw@virginia.edu
Author contributions: T.S., A.D.R., and C.Z. conceived the idea and designed the project. C.Z., T.S., and N.D.P. designed and performed the experiments with assistance from K.F. and A.D.R.; C.Z., T.S., K.F., and N.D.P. designed and built the LPBF simulator. C.Z. carried out the image processing and data analysis and interpretation and proposed and proved the acoustic wave mechanism, with help from all authors. W.T. and X.L. conducted simulations, with input from C.Z. The manuscript was written by C.Z., T.S., and A.D.R. All authors commented on the manuscript.
撰稿:赵 沧
审核:胡楚雄