Associate Professor Dr. Peng Wen and his collaborative team at the Department of Mechanical Engineering, Tsinghua University, developed an innovative architected metamaterial design methodology using a generative architecture design and multiobjective active learning loop (GAD-MALL) combined algorithm. This novel approach has proven effective for the design and optimization of 3D-printed porous metal bone implants, presenting a versatile solution toward solving high-dimensional multi-objective problems with data sparsity and enormity of the search space in metamaterial design.
Architected materials are one of the most widely adopted engineering materials. Due to their excellent mechanical performance and adaptable properties, architected materials are very popular in many fields, such as those of lightweight structures, tissue engineering, battery electrodes, and electromagnetics. Moreover, recent progress in 3D printing has further enabled the customized and inexpensive fabrication of complex material geometries. Despite the broad applicability and immense potential of architected materials, designing them is particularly difficult. The traditional method generally relies on numerical simulation and theoretical analysis which are usually exhausting and time-consuming. Recently, machine learning (ML) has emerged as a promising technique to circumvent this problem and find the optimal solution without any prior knowledge requirements. Furthermore, active learning that combines ML and simulations or experiments to tackle optimization problems is an emerging topic at the frontier of science. However, some of these methods mainly focus on 2D-structure-related problems, while others use Bayesian optimization to solve low-dimensional problems or focus on an unconstrained single objective. The efforts toward solving high-dimensional multi-objective problems are often obfuscated by the data sparsity, the enormity of the search space, and stringent external constraints. For example, porous bone implants should align with the elastic modulus of bone tissue, while also providing adequate compressive strength and biocompatibility; meanwhile, a porous structure comprising 3*3*3 units, with each unit varying across seven porosity levels, can yield an immense 727 potential designs.
The research introduces an inventive integration of a generative model, three-dimensional convolutional neural network (3D-CNN), and numerical simulations within the GAD-MALL algorithm for designing architected metamaterial structures. The process begins with unsupervised learning on a dataset of over 18,000 porous geometries using an autoencoder model to distil high-dimensional data into a low-dimensional latent space representation. Gaussian mixture models are then employed for sampling in the latent space, with the decoder reconstructing the sampled data to new architected metamaterial designs. 3D-CNN models are then used to predict the performance of these new designs and select the designs with high predicted performance, which are subsequently validated through numerical simulations. Through iterative cycles of generation, prediction, and simulation, the GAD-MALL algorithm effectively optimizes the multi-objective performance of the structures. Optimal designs are 3D-printed and experimentally validated, demonstrating significant improvements over conventional designs and confirming the efficacy of this AI-driven design paradigm in addressing the challenges of high-dimensional multi-objective optimization in designing architected metamaterials.
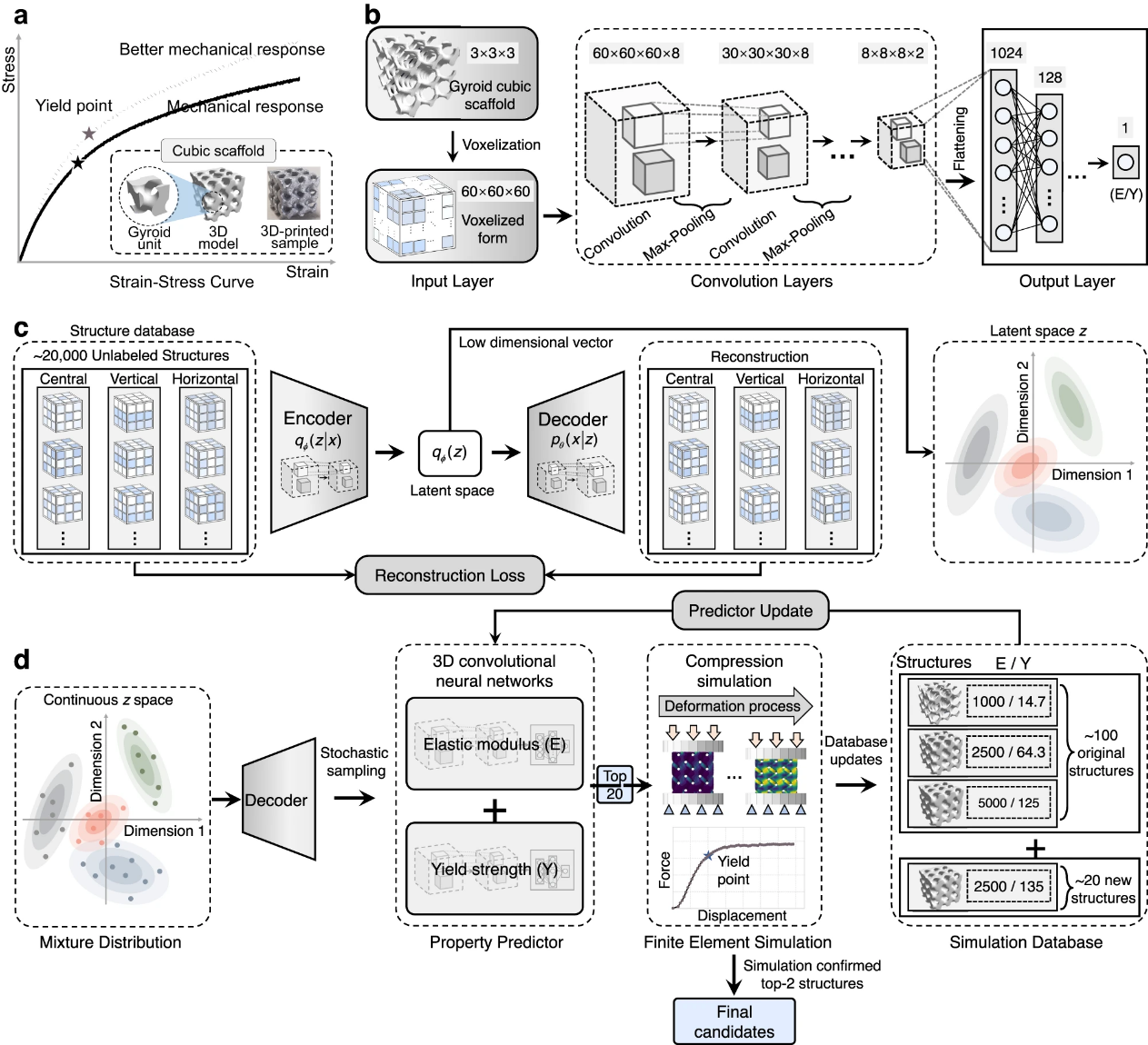
Figure 1. The workflow of generative architecture design-multiobjective active learning loop (GAD-MALL).
The research has utilized the GAD-MALL algorithm to optimize the design of porous bone implants with materials of titanium alloys and biodegradable zinc for the repair of bone defects. The designed implants not only conform to the anatomical morphology and elastic modulus of bone tissue but also retain excellent pore interconnectivity and 3D-printability. Notably, these implants demonstrate superior yield strength and a more homogenous stress distribution compared to both uniform and topologically optimized structures. The team is currently engaged in a collaborative effort with the Department of Orthopedics at Peking University Third Hospital. As a leader in the global forefront of clinical applications for 3D-printed biodegradable metallic porous implants. They have successfully applied these implants in more than 30 clinical cases to address periarticular fracture bone defects. Looking ahead, the team aims to optimize the material composition and structure design of these 3D-printed porous implants through AI-enabled design strategies, aiming to achieve the precision treatment of bone defects.
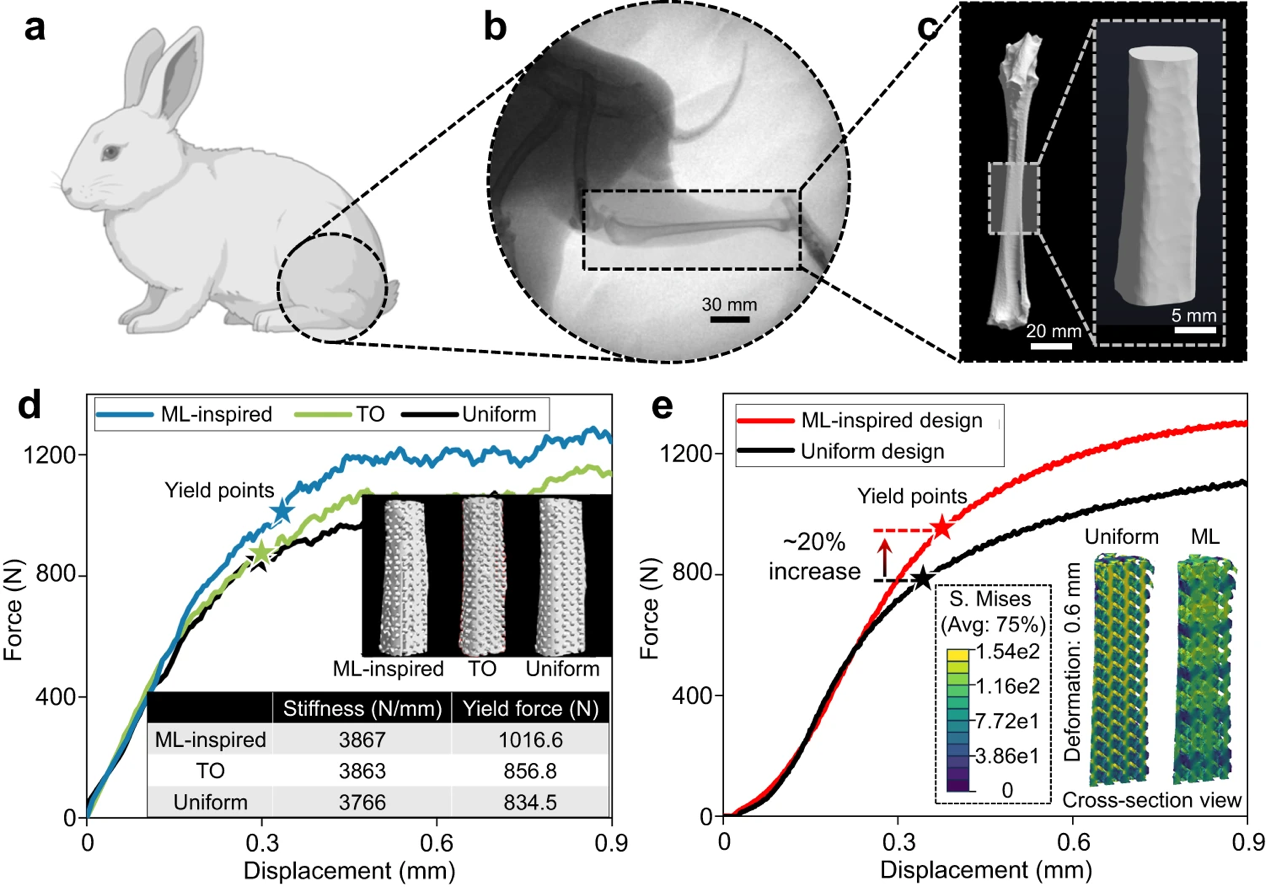
Figure 2. 3D-printed biodegradable metallic porous bone implants with machine learning (ML)-inspired design.
The aforementioned research was recently published in the journal Nature Communications under the title "Machine learning-enabled constrained multi-objective design of architected materials."
Associate Professor Peng Wen, Dr. Ye Wei (postdoctoral researcher at École Polytechnique Fédérale de Lausanne), and Dr. Yu Qin (postdoctoral researcher at Peking University) are the corresponding authors. Bo Peng (Ph.D. student in the Department of Mechanical Engineering at Tsinghua University), Dr. Ye Wei, and Dr. Yu Qin are joint first authors. Other authors include Professor Yun Tian from Peking University Third Hospital, Professor Yufeng Zheng from Peking University, Dr. Liuliu Han and Dr. Yue Li from the Max Planck Institute for Iron Research in Germany, Jiabao Dai and Aobo Liu from the Department of Mechanical Engineering at Tsinghua University. This work was funded by the National Key Research and Development Program of China (2018YFE0104200, P.W., Y.T., Y.Z.), National Natural Science Foundation of China (52175274, 82172065, and 51875310, P.W.), and Tsinghua-Toyota Joint Research Fund (P.W.) and Tsinghua Precision Medicine Foundation (P.W.); Y.W. would like to acknowledge the financial support of the Shuimu fellowship of Tsinghua University.
Link to the article:
https://www.nature.com/articles/s41467-023-42415-y